The United States Pharmacopeia (USP) is a non-profit organization that develops standards for human and animal drugs as well as food ingredients and dietary supplements.
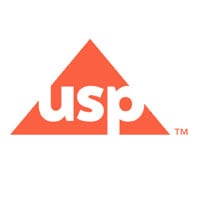
- USP <795> Pharmaceutical Compounding - Nonsterile Preparations
- USP <797> Pharmaceutical Compounding - Sterile Preparations
- USP <800> Hazardous Drugs - Handling in Healthcare Settings
- USP <825> Radiopharmaceuticals - Preparation, Compounding, Dispensing, and Repackaging
These four chapters provide guidelines for safety considerations, personnel qualification and training, facilities and engineering controls, microbiology and surface monitoring, cleaning and disinfection, and much more.
In this blog, we will be taking a look at facility and engineering control guidelines for each of these four USP chapters.
USP <795> provides compounders with guidance on applying compounding practices and does not contain recommendations for engineering controls.
USP <797> states that “a pressure gauge or velocity meter shall be installed to monitor the pressure differential or airflow between the buffer area and ante-area, and the ante-area and the general environment outside the compounding area.” Furthermore, 0.02 to 0.05 in w.c. is the recommended differential pressure to be maintained between two areas in USP <797>.
USP <800>recommends negative pressure rooms to be maintained between 0.01 to 0.03 in w.c. between containment segregated compounding areas (C-SCA) relative to adjacent areas with a minimum of 12 air changes per hour (ACH). For ISO class 7 buffer rooms with an ISO class 7 ante-room, the recommended differential pressure is also 0.01 to 0.03 in w.c., but the recommended ACH is increased to 30.
Lastly, USP <825> states that “the classified areas must be equipped with a pressure-differential monitoring system”, and for positive pressure rooms 0.02 in w.c. between each ISO classified area is recommended. For negative pressure rooms, USP <825> states to refer to the radioactive materials (RAM) license for pressure differential recommendations.
The United States Pharmacopeia (USP) chapters can be found and downloaded from www.usp.org for reference of the complete guidelines.
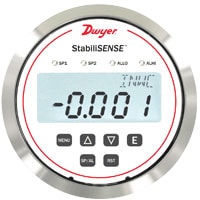
DwyerOmega’s new Series RPME room pressure monitor and Series RPMC StabiliSENSE™ critical room pressure monitor provide the advanced features, high accuracies, and ranges necessary for use with pharmaceutical compounding areas.
The Series RPME room pressure monitor and RPMC StabiliSENSE™ critical room pressure monitor can each be flush or surface mounted in the same size diameter hole as a Magnehelic® gage. This simplifies upgrades from a Magnehelic® gage to the new room pressure monitors. They both come standard with two independent SPDT relays and a 4-20 mA analog output. The RPME contains a piezoresistive pressure sensor, while the RPMC contains a capacitance cell pressure sensor, providing a higher degree of accuracy and long-term stability.
The Series RPME and RPMC are complete systems, allowing for access to pressure, security, calibration, and alarm setup. Visual indication, an easy-to-clean stainless steel bezel, and passcode protection make pressure monitoring in critical applications easier than ever.
If you have any questions, the DwyerOmega Applications Engineers are available to assist by phone at (219) 879-8000 x6402, or by email at tech@DwyerOmegamail.com.