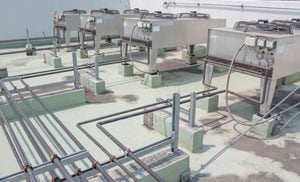
Air flow pressure switches and differential pressure switches work just like the light switches we have in our living rooms at home: when they are switched on, the switch makes contact, closes the circuit, and turns on. When they are switched off, the circuit is broken and power turns off. With air flow switches, instead of being manually switched, the air flow switch closes or opens the contact by reacting to changes in the air pressure at a pre-set actuation point, and turns on and off accordingly. These air pressure switches may be used to start/stop motors or fans, open/close dampers or louvers, sound alarms, and more.
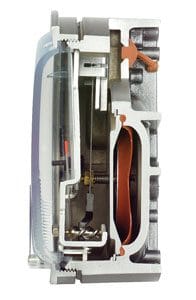
Pressure switches in various combinations are designed to suit unique commercial or industrial needs. Depending on the fluid type, pressure, temperature, ambient temperature, and pressure range requirements, the sensing element technology can be a bellow, diaphragm, or bourdon tube. The sensing material will also vary; it can be made of ceramic, metal, or elastomers.
When the air or gas pressure increases or decreases on both sides of the sensing element, the sensing element moves towards the side of less pressure and mechanically transmits a force to a spring and mechanical linkages. Then, depending on the load exerted on the spring, the switch will actuate. The switch is designed to actuate on either increasing or decreasing differential pressure. The diaphragm motion is resisted by a calibrated spring. This spring determines the range of differential pressure within which the diaphragm motion will actuate the electric switch. The actuation point is set by adjusting the compression or tension of the spring. The pressure that affects the sensing element may be the difference between a positive pressure on one side of the diaphragm and the atmospheric pressure on the other side; a negative pressure and atmospheric pressure; two unequal positive pressures; two negative pressures; or one positive and one negative pressure.
The snap-acting micro switch contacts are either normally closed (NC), or normally open (NO). The normal position of these contacts occurs when there is no pressure applied and thus no pressure is measured by the pressure switch. Once pressure is applied, depending on the switch type, the NO contacts will close or the NC contacts will open. Airflow pressure switches and differential pressure switches are available in Single Pole, Double Throw (SPDT), or Double Pole and Double Throw (DPDT).
What are some applications in which air pressure switches and differentials pressure switches are used?
- The differential pressure switch can be used to prove if the supply fan motor or return fan motors are running on an air handler, or to determine filter status in an air handler.
- As a fan proving switch, the low pressure side would be piped into the inlet side of the blower wheel and the high pressure side would be piped into the outlet side of the same blower wheel.
- Pressure switches are used for fire protection damper control, ventilation duct monitoring, fan overheating protections, fume exhaust systems, etc.
Considerations in Selecting a Pressure Switch
Diaphragm size – The diaphragm diameter determines the sensitivity, which in turn determines the scale. A larger diameter diaphragm will be more sensitive to changes in pressure because it generates more movement than a small diaphragm in low pressure conditions. Larger diaphragms will give a wider increment in the scale and smaller dead bands.
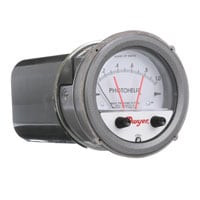
Dwyer Instruments, Inc. offers many series of pressure instruments based on diaphragm size and thicknesses. The Series A3000 and 43000 (in the Photohelic® switch/gage family) offer a large selection of pressure ranges and dead band because of the various diaphragm thicknesses and sizes. They are also offered with different sensing elements to make it compatible for different gases. The Mini-Photohelic® Differential Pressure Switch/Gage, Series MP, has a smaller diaphragm, providing a range up to 20 inches of water. All of the above Photohelic® switch/gages combine the function of a pressure switch with a visible indicating needle dial gage.
Range selection – When selecting a pressure switch, there are many range options. We recommend selecting a range that has a set point (actuation point) as close as possible to the middle of the total adjustment range.
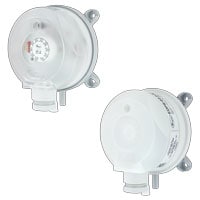
Set point – For service where the set point is known, the unit can be set at the installation point or, for OEM quantities, preset at the factory. Dwyer offers both of these options. For service where field changes in set point are anticipated, the Series A3000, MP, ADPS, EDPS, and 1630 provide a visual set point adjustment for extra convenience.
In cases where pressures may need to be reset to provide a warning, or where the staff technician may need to record the higher or lower value, the Photohelic® Switch/Gage, Series 3000MR, and the Photohelic® Pressure Switch/Gage, Series A3000, are great options. If you need a visual set point and floating contact null switch for high and low actuation, consider the Series 1640. Where two set points are required, choose the Series 1627 or 1831, which have dual switches.
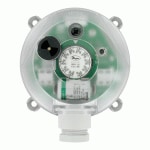
Dead band – For OEM applications, special snap switches are available with an extra wide dead band. Models such as our Photohelic® Pressure Switch/Gage, Series A3000, have dead band ranges from the width of the indicating needle to practically full scale control. The Series ADPS, EDPS, and BDPA have an adjustment knob that allows you to change the set point.
Maximum psi rating – Most diaphragm operated pressure switches are rated for 10 PSI, but our H3 Series is rated for up to 1500 PSI.
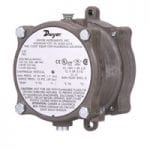
Environments – Many Dwyer pressure switches and differential pressure switches offer explosion-proof housings or weatherproof enclosures for use in harsh environments.
Installation – Select a location that is free of excessive vibration, where oil or water cannot drip onto the switch, and where ambient temperature is around 70°F. Where higher temperatures exist, a coil of copper or aluminum tubing will often provide adequate heat dissipation.
See specification pages for weatherproof enclosures, explosion-proof housings, and environmental switches. As a general rule, differential pressure switches should be mounted with the diaphragm in a vertical plane. It is essential that the set point be adjusted with the diaphragm in the position in which it will be mounted.
Dwyer switches are assembled, calibrated and tested at 70°F (21°C), but the recommended operating temperature can go down to 32 to 130°F (0 to 54°C). With reduced electrical rating, the upper limit can be extended a bit higher. See the specifications of each model for additional information.