As industries such as building automation and water/wastewater become more energy-efficient, powder and bulk is also increasing energy efficiency using pressure transmitters and variable frequency drives. Pressure transmitter demand is also growing due to more stringent regulations in hazardous environments, where remote control and specialty housings must be available.
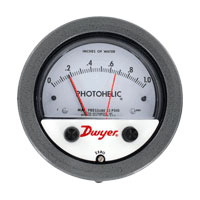
With a typical dust collection system, a pressure sensor (such as our Series A3000 or Series DHII) can measure differential pressure across filter bags. The sensor then sends a switched signal to a timer board (such as the Series DCT500A or DCT1000) to signal a filter cleaning. Pressure in the system is created by a blower, typically positioned near the filter banks on top of the hopper. The system can also use a level switch (like our Series PLS and Series CLS2) to signal a full hopper and possibly open a valve to empty the hopper. So how do pressure transmitters reduce energy consumption? And how can you prevent an explosion in a hazardous environment without the additional cost of specialty enclosures?
Blower and compressor use the most energy
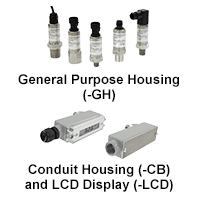
The two main power consumers are the blower and pneumatic pressure via a compressor. Neither can be taken completely out of the system without significant cost (i.e. a new filter cartridge system). Pneumatics have become smarter through use of pressure transmitters (such as our Series 626/628) operating a VFD on the compressor. This equipment is typically provided by a compressor manufacturer or building owner (dust collection OEMs, however, can focus energy savings through the blower operation, either through retrofit or in new installations).
In some cases, the dust collection system will have a duct hood at several workstations. In the machining, welding, abrasives and carpentry industries, the dusts created can be hazardous for workers: metal, magnesium oxide, aluminum oxide and wood dust. In larger shops, dust can form on multiple benches. A collection hood that goes to a central system is cost-effective and vital to the workers’ health as well. Workers at a station can open a damper to allow the dust to be collected. When workers aren’t present, the damper stays closed to prevent suction from being reduced at other stations. Otherwise, CFM and duct pressure would constantly change due to the volume of air changing in the system. The blower is typically running at full speed. When the duct system has a majority of dampers closed, the blower works hard against a larger resistance, creating more of an energy load. How can the blower run with more energy efficiency?
Monitoring duct static pressure provides the most cost-effective solution
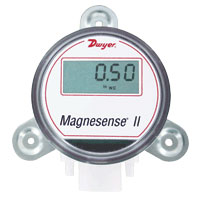
VFDs are now being added to the blower operation on newer systems, especially systems that run for several hours a day. Determining whether each damper was open or closed due to a position switch would make a system very complicated. So the most cost-effective solution has been to monitor duct static pressure. Dwyer’s MS and MS2 Magnesense® differential pressure transmitters and 616W differential pressure transmitter have become very widely used in this case. All are available in ranges typically used, such as 10″, 15″, 20″ and 25″ w.c., and are standard in NEMA 4X housings. Of course, the duct requires a pressure sensor. Dwyer’s A-491 static pressure sensor has performed well in dust-filled environments. These make installation a breeze in both new and retrofit projects.
The transmitter will send an analog signal to the VFD to modulate the blower to the static pressure within the duct system. When more dampers close, the static pressure increases. Therefore, the blower will lower its rpm to maintain an efficient system pressure. This dramatically reduces the power consumed, easily seen on systems running several hours each day.
Increase safety in hazardous environments
Another application growing in popularity is explosion-proof pressure transmitters that monitor DP across filter bags in hazardous environments (i.e. coal dust, grain dust and processes where methane may be a byproduct).
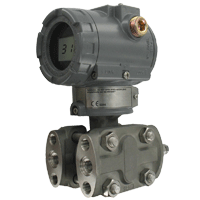
This application sends a signal to a PLC for pulse valve control. Regulations have gotten more strict than they typically were regarding the use of explosion-proof or intrinsically safe devices in these applications. Dwyer’s Series 3100D differential pressure transmitter has been ideal for this application. It’s standard explosion-proof for Class 1, Div. 1 and offers a more cost-effective solution than comparable products. The Series 3100D internally allows for an analog output to a PLC as well as another remote display. This can make it easier to read the differential pressure in a reachable location on a large collector rather than the top of the collector. The signal can then be sent outside of the hazardous location to a PLC panel. If the collection is a n on-hazardous location, a differential pressure transmitter such as the 616W, MS, or MS2 may be used as discussed earlier when dealing with static pressure.
Rising energy prices and stricter agency regulations are increasing the use of pressure transmitters. Both require high accuracy, low cost solutions.