In industrial environments, stability refers to a system's ability to maintain consistent performance over time under normal operating conditions. This includes everything from pressure sensors to flow measurement devices to control instrumentation.
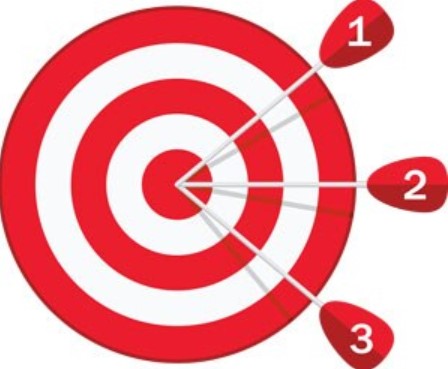
Stability is especially critical in sectors where precision and safety are paramount - such as pharmaceutical manufacturing, semiconductor production, and cleanroom environments. In these settings, even small deviations can lead to contamination, equipment failure, or regulatory non-compliance.
How Stability Enhances HVAC Efficiency, Longevity, and Air Quality Compliance
Stability improves HVAC system performance by increasing overall efficiency and reducing the need for costly maintenance. If an air handler, VAV system, or chiller/boiler system is running inefficiently, components are more likely to wear and break down faster than in a more efficient system. Beyond equipment longevity, stable HVAC performance is essential in manufacturing environments where temperature and pressure differentials directly impact product quality, employee safety, and energy usage.
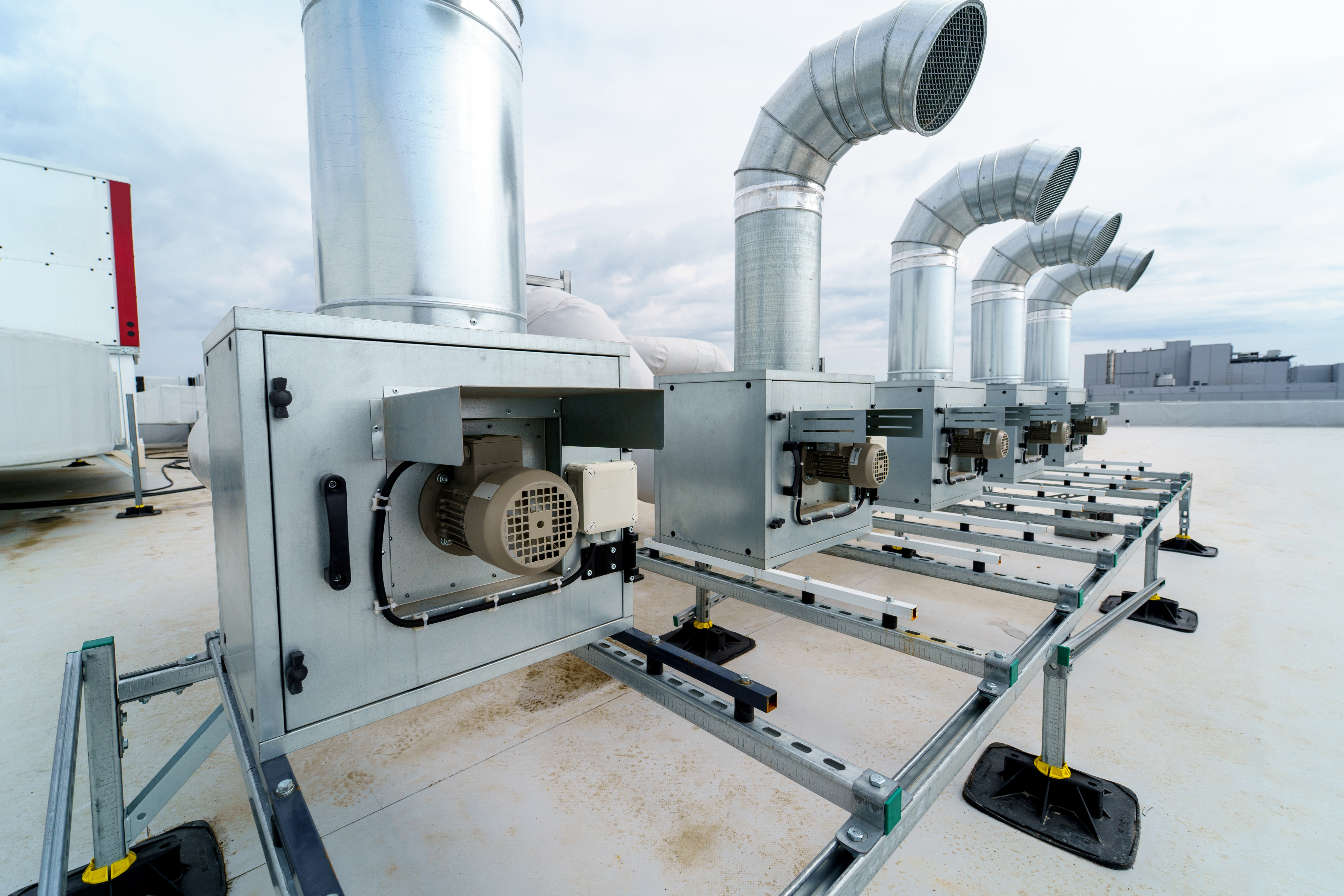
For example, in cleanrooms or pharmaceutical processing spaces, maintaining a consistent differential pressure between zones prevents airborne contaminants from migrating into critical areas. In these cases, even minor fluctuations in pressure can disrupt airflow balance, violate compliance standards, or compromise sensitive operations. Precision control instruments (especially those that combine sensing, display, and control functionality) are key to achieving and maintaining these stable conditions.
The reduction in downtime associated with maintenance and recalibration is another benefit of stability. Stability helps to ensure full production capacity and can be recalibrated on a scheduled date/time that corresponds to a plant shutdown/plant maintenance schedule.
Stability also ensures patient rooms are available and not out-of-calibration, which is especially useful in healthcare facilities with an above average patient capacity. In critical environments, stability ensures safety standards are maintained.
Stability in Semiconductor Cleanrooms: Protecting Yield Through Pressure and Humidity Control
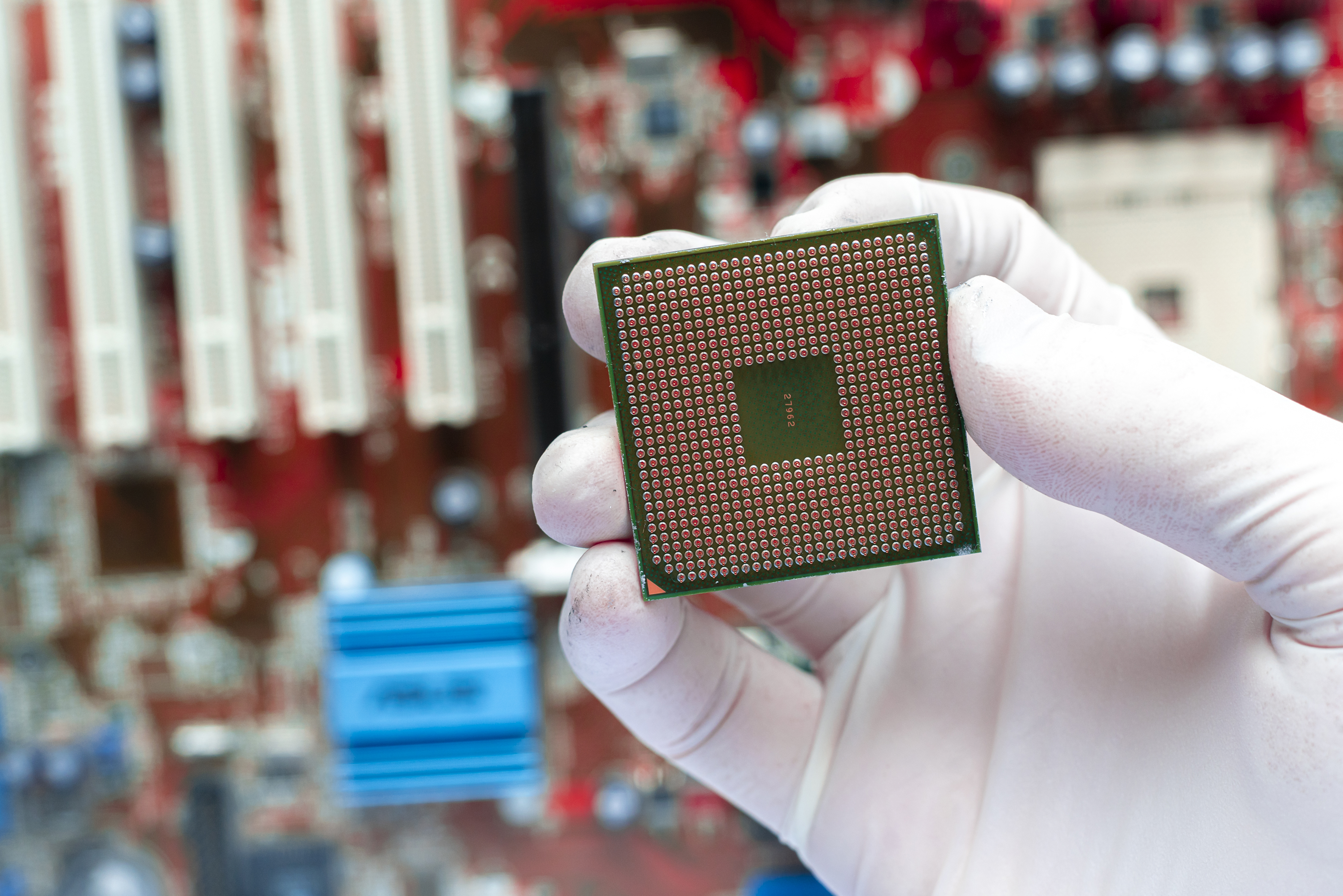
If pressure, temperature, and relative humidity (RH) are not maintained properly in semiconductor manufacturing areas, it can result in the infiltration of dust and particulates due to inadequate differential pressure, sudden shifts in RH, or temperature fluctuations. All of these can damage sensitive wafers or disrupt lithography processes. Stability is not just a matter of operational efficiency in these environments; it is critical to yield, reliability, and regulatory compliance.
Semiconductor fabrication depends on meticulously controlled cleanroom environments where even microscopic variations can lead to defects, contamination, or unplanned downtime. Maintaining stable differential pressure between clean zones, process bays, and service chases ensures that airflow consistently pushes contaminants away from critical spaces. Achieving this level of stability requires highly responsive instrumentation that can monitor and control pressure conditions in real time, ideally with integrated alarming and automation-ready outputs.
Pharmaceutical Manufacturing: Meeting CGMP and Contamination Control Standards
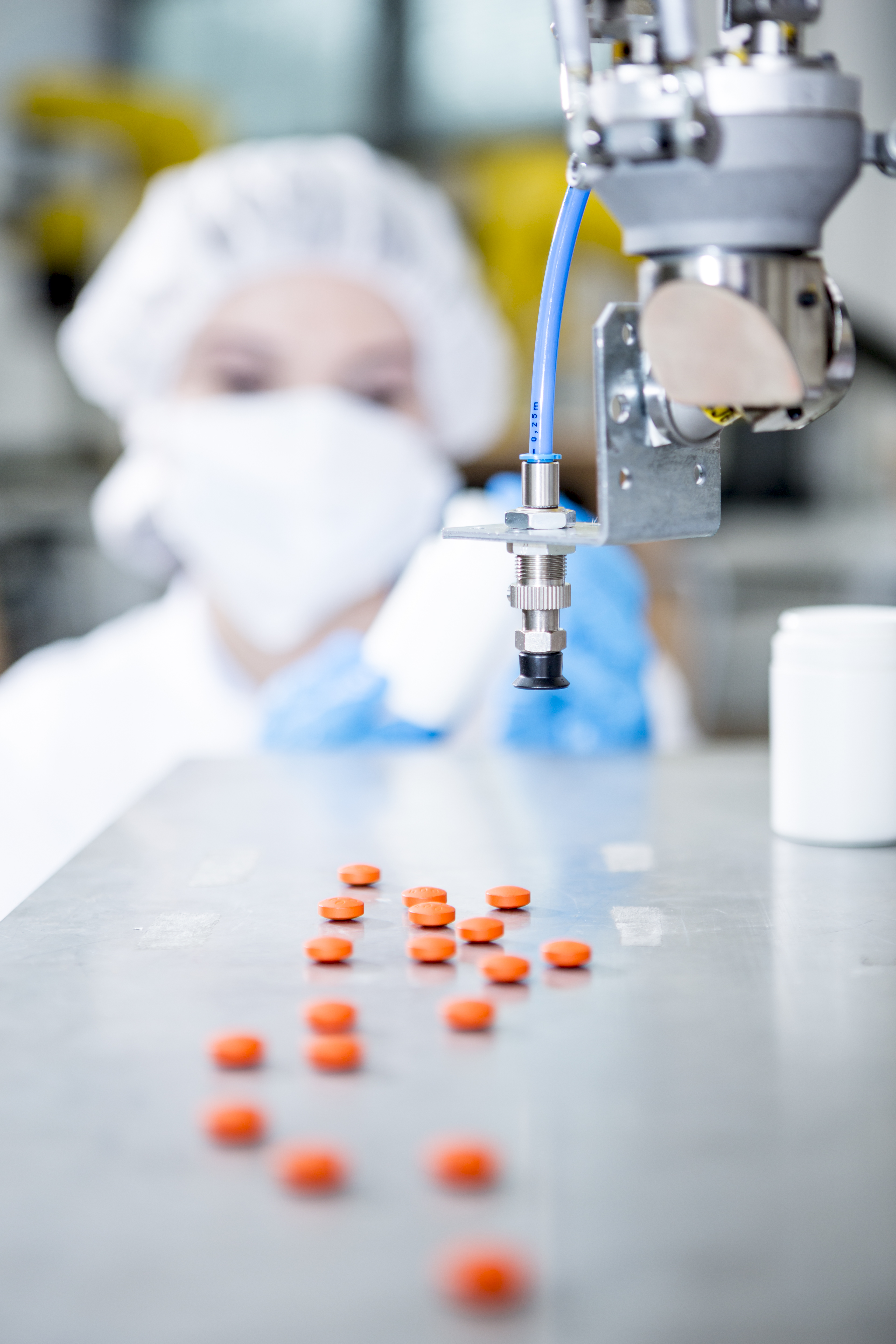
Infiltration of airborne microorganisms due to insufficient differential pressure, sudden spikes or drops in RH, or fluctuations in temperature can render drugs unsafe or create unsuitable conditions for formulation and storage.
Ensuring environmental stability in these spaces is not optional, it is foundational to product safety and public health. Differential pressure plays a central role in maintaining directional airflow between clean and less clean zones, helping to prevent cross-contamination during material transfer, preparation, or packaging. Reliable differential pressure controllers that offer real-time monitoring, integrated switching, and alarm functionality are crucial for meeting strict pharmaceutical standards and ensuring continuous environmental compliance.
Stability for Infection Control and Patient Safety
Lastly, the infiltration of viruses, bacteria, or pathogens from or into an isolation room, clean room, and/or operating room is a major concern when it comes to protecting both patients and healthcare personnel. Maintaining a proper differential pressure in these critical healthcare environments is essential to preventing the spread of airborne infectious microorganisms, particularly in settings involving immunocompromised patients, surgical procedures, or infectious disease containment.
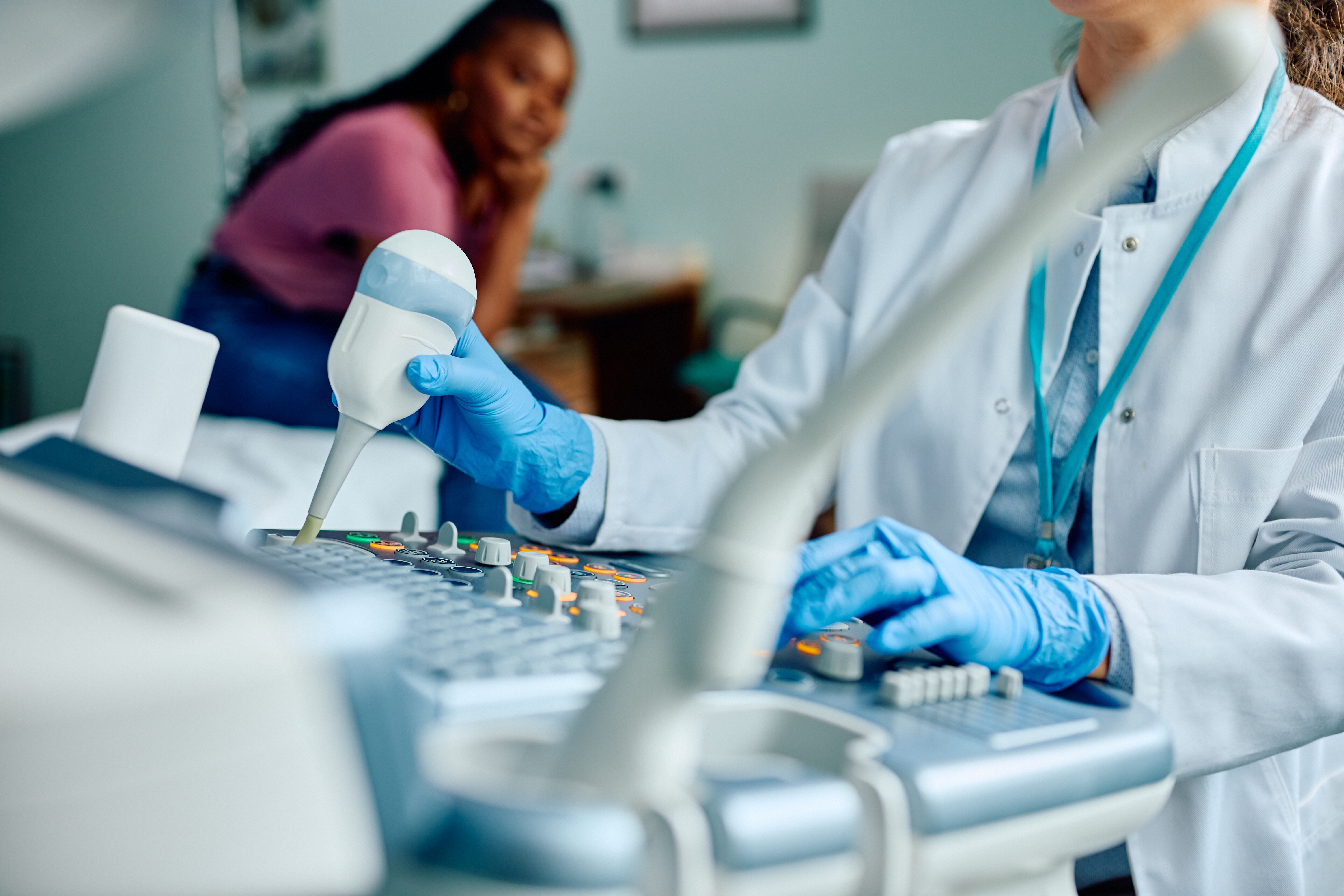
Stable pressure control ensures that negative pressure rooms (used for isolating contagious patients) consistently pull air inward, preventing contaminants from escaping. Conversely, positive pressure rooms (such as operating suites or protective environments) must push clean air outward to block contaminants from entering. Any instability — such as pressure drops or fluctuating airflow — can compromise the protective barrier and elevate the risk of hospital-acquired infections (HAIs).
To maintain this stability, healthcare facilities rely on differential pressure monitoring systems that offer continuous real-time readings, local display, and alarm capabilities to alert staff when conditions deviate from safe thresholds. Devices like the Digihelic® Differential Pressure Controller integrate these features into a compact, reliable platform ideal for mission-critical healthcare applications.
The Series-DHC Digihelic® Differential Pressure Controller
A DwyerOmega Solution
The Series-DHC Digihelic® Differential Pressure Controller provides a stability rating of less than ±1% full scale per year. The DHC is a 3-in-1 instrument offering a digital display gage, control relay switches, and a transmitter with both current and voltage outputs.
The Digihelic® controller is the ideal instrument for pressure, velocity, and volumetric flow applications reading in several commonly used engineering units with optional unidirectional or bidirectional ranges. These units achieve a 1.5% or better accuracy on extremely low ranges, and 0.5% accuracy for ranges at or above 1 in w.c.
Contact a DwyerOmega Expert Today!