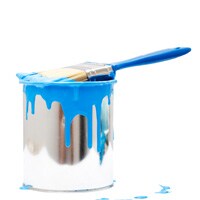
Jaguar. Ford. Ferrari. Three iconic automakers with storied racing pedigrees that have made some of the fastest and most beautiful cars in the world, each draped in a coat of paint of their own signature color: British Racing Green, Ford's Grabber Blue, and Ferrari's Rosso Corsa.
Beyond providing a bit of personality and character, a car's paint also serves a practical purpose: protecting the body, frame, and other components from the elements, preventing rust and corrosion from destroying the raw material underneath. The earliest paint jobs were done by craftsmen such as furniture makers and carriage builders who applied varnish primers and oil-based enamel paints by hand. These finishes were inky, with low opacity and coverage, requiring multiple coats and lengthy drying times. And even with all that work involved, the paint would soon become brittle and start chipping away.
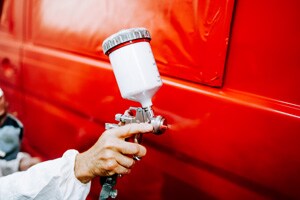
The key to applying paint as effectively as possible is to control every possible variable. Enter the paint booth: a controlled environment where the temperature, humidity, and air flow are controlled to optimize paint delivery and curing. And it's not just the atmospheric conditions that must be controlled, the temperature of the paint itself affects its viscosity. If the paint is too cool and thick, it won't flow through the sprayer correctly; too warm and thin, and it won't provide enough coverage in a single coat.
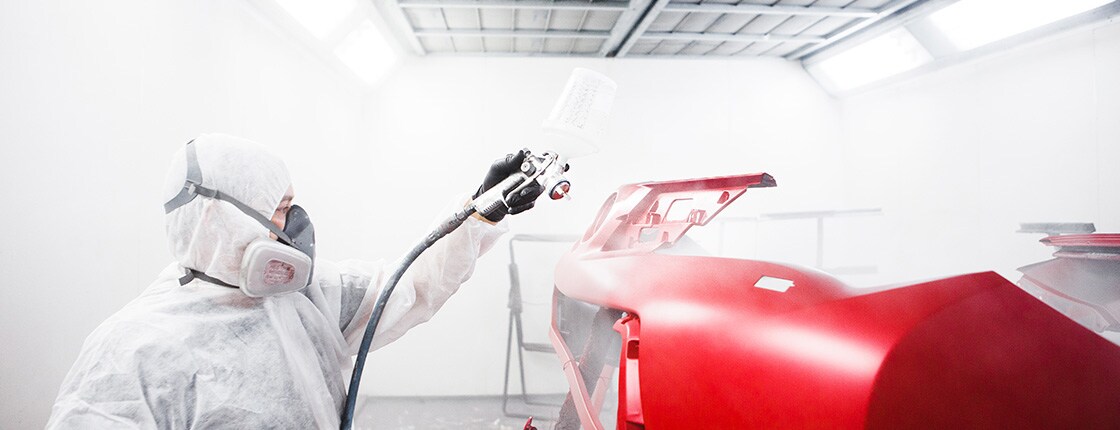
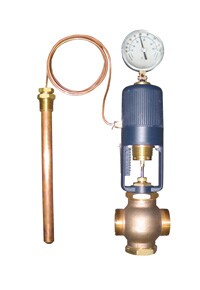
The most advanced paint booths use heat exchange systems, where warm or cold water is pumped through a series of lines running through a tank that heat or cool the surrounding liquid, in this case paint. This ensures that the paint is the ideal temperature when it reaches the nozzle.
The Series 38Rself-acting temperature control valve is the perfect device to monitor and automatically control temperatures in paint booth heat exchange systems. The Series 38R's heavy duty, die-cast aluminum fail-safe actuator and over-range protection ensure a long and reliable service life, and with no power supply required, it's easy to install.
For more information on the Series 38Rself-acting temperature control valve, or any other DwyerOmega products, the DwyerOmega Applications Engineers are available to assist by phone at (219) 879-8868 x6402, or by email at tech@DwyerOmegamail.com.