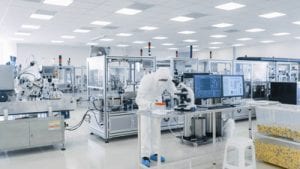
The purpose of a clean room is to limit the number of particulates in a clean space. These particulates can be any type of sub-micron particles, such as dust, pathogens, chemical vapors, or moisture droplets. Clean room manufacturing areas are used by many industries to produce semiconductors, pharmaceuticals, medical devices, etc.
Maintaining a proper differential pressure between the clean room and the exterior area is the most crucial aspect of keeping the clean room “clean”. To understand why sensor stability is important to these critical applications, it is important to also understand why a pressure difference is needed.
Why is a Pressure Difference Needed in Clean Rooms?
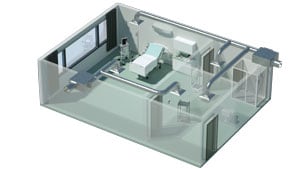
A pressure difference between a clean room and the anteroom, or the room immediately outside the clean room, is needed to ensure low to no infiltration of unwanted particulate matter into the clean room.
If a clean room is kept at a positive pressure in relation to the anteroom, it will force all air (and particulate matter) out to the anteroom. If you have ever walked into a building and noticed a draft coming from inside the building to the outside while blowing the door open, you have experienced a building under positive pressure in relation to the outside. In this case, the door was likely difficult to close because of the high-pressure differential.
How are Sensors Tied into Clean Rooms?
Positive pressure in clean rooms is maintained by a fan, or blower, typically within a VAV (variable air volume) system that increases the amount of air provided into the clean room. The more air provided into the room, the higher the air pressure in it.
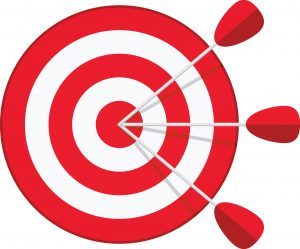
A differential pressure sensor, like a room pressure monitor, room status monitor, or a simple differential pressure transmitter, measures the pressure difference between the cleanroom and anteroom. It then provides the measurement to a DDC (direct digital controller) that controls the VAV system. If the pressure is too low, the VAV system will provide more air; if the pressure is too high, the VAV system will limit the amount of air it pumps into the room.
Since the pressure that is to be maintained is relatively narrow (0.02-0.05” w.c.), it is important that the differential pressure sensors maintain their accuracy over time. In other words, the sensors need to have excellent stability.
If stability is not maintained and the pressure sensor drifts, becoming inaccurate over time, the VAV system will either provide too much or too little air. As a result, the positive pressure of the clean room can be compromised. Particulates will then be able to enter the clean room and damage or destroy the goods being manufactured in that clean environment.
What Other Parameters Need to be Maintained in Clean Rooms?
Depending on the type of clean room and specific application, other environmental parameters besides differential pressure will also likely need to be maintained. Additional parameters could include:
- Temperature
- Relative Humidity (RH)
- Air Changes per Hour (ACH)
- Volatile Organic Compound (VOC) Levels
Conclusion
Using sensors with high stability will help to ensure clean rooms meet quality and safety standards. Stability will help ensure that safe levels for all clean room applications, including pharmaceutical, semiconductor, and medical device manufacturing, are maintained.
To learn more about stability and why it is important, read our previous blog articles listed below: