Why do the inlet and outlet pressure of pumps need to be monitored? What issues may be encountered if they are not monitored?
Air compressors, irrigation systems, and heat exchangers all use pumps to push air or water through their systems. If the pressure in any of these systems is too high or too low, it could have serious consequences for the pump, the pipes, or the entire system. Most engineers choose pumps that operate 80-110% of their Best Efficiency Point (BEP), the point on the curve where the pump is most efficient. Pump performance will suffer if the pump is operating outside of the BEP, so it is important to monitor pressure to ensure you are getting the most out of your pumping system.
There are two key types of pumps: positive displacement and kinetic energy (most commonly known as centrifugal).
In positive displacement pumps, a fixed amount of fluid is trapped and mechanically displaced in to the discharge pipe. Overpressure is a serious concern in applications with positive displacement pumps because of dead head situations; essentially, the pump will not shut off and will continue to generate pressure even when there is no flow. Because the pumps do not shut off, the pressure will climb, potentially leading to a pipe burst, pump lock up, broken pump shaft, or overheated motor. This is dangerous for anyone working near the pipes and could result in high maintenance and material costs if something were to break.
Centrifugal pumps have an impeller that rotates within a volute (a curved funnel that increases in area as it approaches the discharge port). The impeller has multiple blades mounted on a shaft that projects outwards in the volute. Because the inlet is positioned in the center of the impeller, when the impeller rotates, centrifugal force pushes the fluid outwards from the center, creating a vacuum in the inlet. The fluid is then pushed into the pump volute walls. This process converts rotational, kinetic energy to pressure and pushes the fluid through the outlet at a high velocity. When centrifugal pumps are operated outside of the BEP, the impellers are subject to asymmetrical forces, which manifest in mechanically unstable conditions, including: high vibration levels, excessive hydraulic thrust, increased temperature, or erosion. After the pressure rises to the dead head point in centrifugal pumps, the water flow will stop. Even though there is no risk of a burst when a centrifugal pump overheats, there will be no flow to dissipate the heat and this will consume a lot of power and waste money.
There are also problems that can affect all pump types. For example, if there is a valve failure or clog in the inlet side of the pump, it will starve the pump; it will not have any fluid to push through. In a starving pump, the fluid heats up and could destroy the pump seals. Starving pumps can be recognized through low pressure on both the inlet and outlet sides. Similarly, if a pump system was not primed upon startup, there will be no flow, therefore no heat relief, and there will be no or very low operating pressure on both the inlet and the outlet. This situation will cause the pump to fail quickly. With a broken pump shaft or failed motor, the pressure seen on the inlet and outlet will be the same as the static pressure.
Some newer pump systems that have variable flow pumps, and/or modulating valves will have problems with cavitation (i.e. the formation of empty spaces within the fluid and pumps). The formation of bubbles in the fluid generates heat and vibration that can destroy pumps. Luckily, the minimum flow rate at which cavitation starts is available before pump selection/purchase. If the pump inlet pressure is monitored and kept above this minimum head pressure, there is little risk of cavitation.
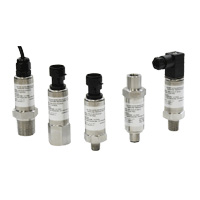
Monitoring pump inlet and outlet pressure is very important for the safety of workers and for the protection of the pumping system itself. A great way to measure pump pressure is with pressure transmitters that can convert pressure readings into analog for easy measurement. The Dwyer Industrial Pressure Transmitters, Series 626 and 628, detect the discharge pressure, inlet pressure, over pressure, and under-pressure of an exchanger or pump which can then be used to determine the flow performance of a system.
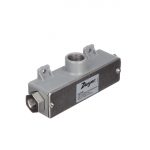
Differential Pressure Transmitters, Series 629C, measure the differential pressure in compatible gases and liquids. All Dwyer pressure transmitters are appropriate for measuring tasks in commercial, industrial or potable water applications and can monitor differential pressure in applications such as air handlers, chillers, heat exchangers, and hydraulic systems. Regardless of the type of pumps used, pressure transmitters help track the inlet and outlet pressure of pumps to determine if pressure seems abnormal before something goes wrong and the system is permanently damaged.