Dwyer Instruments offers many types of flow measuring products including orifice plates, which are used as a flow sensing element with a differential pressure monitor.
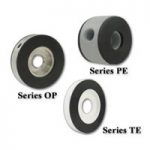
Orifice plates are a primary flow element, detecting the flow of a fluid passing through the plate by sensing the pressure drop across the plate. When a fluid flows through a restriction in a pipe, it creates a pressure difference between upstream and downstream of the restriction. This pressure difference is proportional to flow rate according to Bernoulli’s principal, similar to a Pitot tube. Orifice plates are commonly used as they are simple to use, low cost, work with gases or liquids, and require low maintenance. Adversely, they do have large pressure losses with about 50% of the pressure drop not recoverable. Continue reading “Flow Measurement with Orifice Plates”