When it comes to capturing energy savings, owners, contractors, and engineers will utilize several design efforts to reduce a building’s total energy consumption and carbon footprint. The first area that design engineers typically tackle is the lighting design of the building (using things such as building orientation to maximize natural light or low energy consuming LED lights), but another large consumer of energy in a building is the ventilation system used for garage parking.
In the United States, the bulk of automobiles sold utilize a combustion engine, which in turn produces a potentially harmful and dangerous gas, carbon monoxide (CO). In fact, all enclosed parking garages in North America are subject to ventilation standards established by the International Mechanical Code (IMC) and the American Society of Heating, Refrigeration, and Air-Conditioning Engineers (ASHRAE) to help ensure the safety of those using the parking garage. IMC and ASHRAE have developed standards that require garage ventilation systems to run continuously during building occupied hours, with an exception made for those that deploy carbon monoxide sensor based demand controlled ventilation (DCV) systems.
So what exactly are demand controlled ventilation systems (DCVs) and how do they help to reduce energy consumption in a parking garage? Simply put, this system involves running equipment only when there is demand on the equipment or increasing volumes of carbon monoxide present. This could occur during the morning, lunch, and evening hours when tenants or employees are entering/leaving the parking structure in their vehicles thus increasing or decreasing CO levels.
The first and simplest form of demand control ventilation systems integrates a carbon monoxide switch. These devices monitor the CO levels in the parking structure. Once they begin to reach an unsafe level, the relay contacts energize and run the exhaust fans until the CO levels decrease to safe levels, then de-energizing the relays and turning off the fans until CO levels increase again. While this helps to reduce the energy consumption in the building by only running fans when they are needed, the drawback to this design is that the fans are running at full speed when CO levels exceed the setpoint consuming more energy.
A more energy efficient solution would be to incorporate a variable flow demand (VFD) control ventilation system. This type of system is designed to keep the garage fans running continuously and vary motor speeds based on CO concentrations in the garage. In this system, a carbon monoxide sensor feeds PPM levels to a building management system (BMS) or garage control panel through an analog output, current or voltage, or BACnet or Modbus communications. The BMS or garage control panel then takes this input to control the speed of the VFD and fans by ramping up or slowing the fan speed based off of a control setpoint programmed into the BMS or garage control panel.
The VFD is varying the speed of the motor feeding the exhaust fan by changing the frequency of the electric power going to the motor. This process significantly decreases the energy consumption of the fans. For example, a VFD running a three phase motor at 50% of its full load capacity reduces the energy required by that motor by 80%. These designs also help to increase the usable life of the motors and fans by not running those fans at 100% capacity consistently.
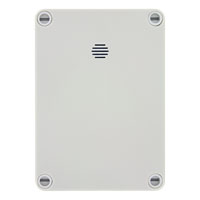
Dwyer understands the importance of energy conservation and offers a number of carbon monoxide sensors to meet any budget and the two varying tiers of demand control ventilation. The CMS300 offers an integral relay which can be used for maintaining setpoint values of 25, 60, or 150 PPM making it a low cost option to start incorporating the cost saving benefits of demand control ventilation.
If incorporating a variable flow demand control ventilation system, the Series GSTA or GSTC are great options for providing a linear analog (GSTA) or linear communication (GSTC) signal to the BMS for controlling variable speed drives and fans. For larger parking structures, the BACnet or Modbus communications can greatly reduce the amount of wiring necessary by daisy-chaining sensors together and back to the BMS.
To learn more about Dwyer’s offerings of gas sensing instrumentation that can be used for monitoring carbon monoxide levels in parking garages, please contact us at 219-879-8000 or tech@dwyermail.com.