Commercial Refrigeration Thermostats Go Digital for Greater Control
In the past, bulb and capillary mechanical thermostats were used in chillers to maintain proper water temperature. As technology has advanced, digital temperature switches have replaced many mechanical ones because a digital temperature switch provides the same functions while also serving as a timer, external relay and thermometer. Where are digital temperature switches used, and which features have caused the conversion?
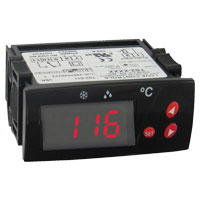
Simple Digital Temperature Switches Cycle Compressor and Evaporator
The most popular type of digital temperature switch features a single input and a single output. These control the process temperature by cycling a compressor, which compresses the refrigerant gas in a system. The hot, compressed refrigerant gas then flows from the compressor to the condenser. The condenser acts as a heat exchanger, using ambient air to cool the refrigerant gas. As the refrigerant gas cools, it becomes a cold liquid-gas mixture that is cycled to the evaporator. The evaporator, acting as another heat exchanger, typically transfers heat from ambient air, water or a water-glycol mixture to turn the refrigerant back into hot, low-pressure gas to feed the compressor. At the evaporator stage, the refrigerant can be cold enough to drop the temperature of the water flowing through the evaporator close to its freezing point. The evaporator fan pulls air across the cold evaporator coils to refrigerate the cabinet.
No Defrost Timer Required
Like their digital counterparts, mechanical thermostats are able to turn on the compressor based on the temperature inside the supply line, but they require a defrost timer to allow the evaporator coils to defrost. If the evaporator coils don’t defrost, water flowing through the evaporator lines can become obstructed, causing the water to freeze and damage the evaporator.
Single input/single output digital temperature switches have a built-in timing function that eliminates the need for the defrost timer. The built-in defrost timing function allows the user to define the defrost cycle time and how frequently the system should defrost.
Since external temperatures can affect how fast the coils defrost, a second temperature input probe is available on higher-end digital systems to turn off the defrost cycle when the temperature reaches a desired level. To perform this function, the defrost temperature probe is normally mounted close to the evaporator coils.
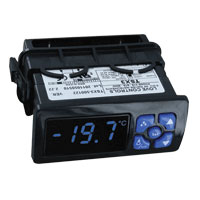
Multiple Relay Outputs Give Tighter Control
Most digital temperature switches are available with multiple relay outputs to allow even better control of the chiller. The primary relay continues to control the compressor as in the previous application example. The second relay is normally used for applications that require either a gas or electric defrost. These applications tend to require shorter defrost periods due to the sensitivity of the stored products or for applications in which the ambient air conditions are not ideal for defrosting the evaporator. Additional relays can be used to control an alarm or a fan control when combining the chiller operation with a make-up air unit.
No Thermometer Needed to Read Temperature
Since most mechanical thermostats don’t have a display, most commercial chillers also required a bimetal or gas-filled thermometer to display water temperatures. Digital temperature switches, on the other hand, have a bright LED display that is easy to read in dark areas. This display reduces labor and material costs by eliminating the bimetal thermometer, the extra connection to the pipe and, most importantly, the labor of installing the thermometer.
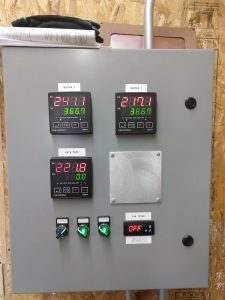
Software Offers Additional Benefits
The software installed in microprocessor-based digital temperature switches offers additional benefits such as minimum compressor on and off time, which is the most commonly used. These safeguards protect the compressor against chatter and premature wear. Digital temperature switches also offer ambient temperature probe adjustments that allow you to correct temperature readings. These adjustments can compensate for temperature errors due to the resistance of the extension wire on applications where the temperature sensors are mounted long distances from the control.
Overall, digital temperature switches reduce costs by eliminating other components, increase system efficiency and offer more user-friendly options. And as digital control technology continues to advance, digital temperature switches will increasingly replace mechanical switches.
See Dwyer’s full line of digital temperature switches and digital temperature process controllers to see how you can gain greater control and efficiency.