Level detection applications are one of the most interesting things we do at Dwyer as there are so many types of switch technologies. Even just for powder and bulk level detection, there are many ways to sense the level. Dwyer offers several different technologies for powder and bulk solids point level detection. These include: diaphragm, paddle, tilt, capacitive, and vibration. So if you’re wondering how to determine which technology is best for your application, here is a simple guide to help you select the proper technology.
Diaphragm Switches
The oldest and simplest of these level technologies is diaphragm switches. These switches are installed in the side wall of the vessel from the outside using a flange, or are installed from the top of the vessel by being suspended on a pipe. The switch actuates as the material height increases in the vessel and the weight of the product presses against the diaphragm. When the material level decreases past the diaphragm, the switch reverts to its normal state.
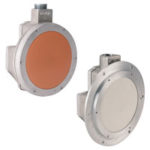
The Ultra Mag™ explosion-proof level switch is an example of diaphragm technology. This series uses a unique magnetic linkage which isolates the electrical compartment from the process material, thus reducing maintenance, improving sensitivity, and making the unit very reliable.
Advantages: The units are flush and do not have a probe that extends into the vessel. Where a probe or paddle from other types of sensors can be easily broken off, this makes them well-suited for materials that are heavy, flowing, or have a large particulate size. They also do not require calibration or a power supply.
Disadvantages: They are pressure sensitive; so a breathable diaphragm or venting must be used for applications with pressurized vessels. They are also a mechanical device with a diaphragm that will wear with use over time.
Paddle Level Switches
Paddle switches are the most common way to detect powder and bulk level. This type of switch is installed in the side wall of the vessel from the outside using a flange, or installed on the top of the vessel with an extension pipe. These units incorporate a motor that rotates a paddle inside the vessel. As the material height increases in the vessel covering the paddle, the weight of the material stops the paddle from rotating, turns off the motor, and actuates the switch. When the material level decreases past the paddle, a spring starts the motor again and the switch reverts to its normal state.
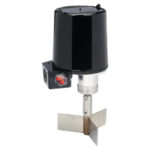
The PLS paddle level switch features a magnetic drive that isolates and completely seals the control head from the process and environment preventing material or dust from entering the control head, both reducing maintenance and increasing reliability. Additionally, the magnetic drive creates a non-mechanical slip clutch that prevents damage to the motor and drive mechanism from sudden or excessive loading on the paddle.
Advantages: This is a low cost technology. They are easy to use as there are no electronic calibrations needed for the application and they are versatile in application usage.
Disadvantages: They are mechanical and the motor will wear with use, it will not work with very light materials, and the unit must be purchased according to the power supply being used.
Tilt Level Switches
Tilt level switches are used for high level indication as they are installed suspended on a cable or chain above the material being sensed. As the material height increases and comes in contact with the probe, the material pushes the probe to the side and tilts it. When the probe is tilted at approximately 25 degrees, a ball on the inside rolls off the contact and actuates the switch. When the material level decreases, the probe falls back to being vertical and the switch reverts to its normal state.
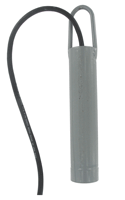
The LTS tilt switch probe offers a switch contact that is mercury free and comes in steel or 316 SS.
Advantages: This technology is very advantageous for open storage applications where it would not be possible to mount a fixed sensor. They are also very good for large particulate materials.
Disadvantage: They are mechanical and will wear, will only work for heavy products, and are mounting specific.
Capacitive Level Switches
Capacitive level switches are very good for a wide variety of applications as they can be used for liquids and powder and bulk solids. This type of switch can be installed in any position and the probe can be shortened or lengthened to almost any measurement needed. Capacitive level sensors determine the level of material by changes in probe capacitance resulting from the movement of dielectric materials between the probe and the reference ground, such as a tank wall. As material height increases and comes in contact with the probe, the capacitance changes from the normal calibrated state and the switch actuates. When the material level decreases, the probe again senses the capacitive change and the switch reverts to its normal state.

The CLS2 capacitive level switch offers several features, including: automatic calibration, universal power supply, coat guard, external switch indication, and a failsafe setting.
Advantages: They are non-mechanical so there are no parts to wear, jam, break, or need routine maintenance. This technology is very good for coating materials as it is immune to product build up on the probe. They are also good for high pressure vessels and when the bulk density can change.
Disadvantages: They have to be calibrated for the application and can be thrown off by different dielectric materials in one vessel if not calibrated properly.
Vibration Level Switches
Vibration level switches are very sensitive and very good for light materials. This type of switch is installed in the side wall of the vessel from the outside, or installed on the top of the vessel with an extension pipe. Tuning fork level switches incorporate a piezoelectric crystal that vibrates the fork at its natural frequency. As material height increases, the fork comes in contact with the material dampening the vibration and actuating the switch. When the material level decreases, the fork becomes free of material and the switch reverts to its normal state.
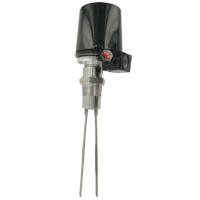
The TFLS tuning fork level switch features a universal power supply, external switch indication, adjustable sensitivity, and a failsafe setting.
Advantages: Vibration switches do not need to be calibrated for dielectric constant or bulk density making installation and set up easy. They are ideal for light powders sensing lower than any of the other technologies, down to 1.8 lb/cu ft (30 g/l).
Disadvantages: They are not good for coating applications, the probe can be physically damaged resulting in the unit not functioning, and this is the most expensive technology.
Be sure to remember that the selection of the technology for your application will depend on many factors such as material properties like flowability, abrasiveness, chemical compatibility, temperature, particle size, stickiness, etc. as well as application properties or environmental needs such as being explosion-proof, the pressure of the vessel, and the location of the sensor.
Please reach out if you have any questions about selecting a level monitoring solution. The Dwyer team is always happy to assist with any of your needs and can be reached via phone or email.