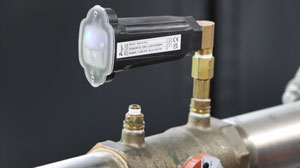
Dwyer’s Series 490W Wireless Hydronic Differential Pressure Manometer is the most accurate and easy-to-operate manometer on the market. Along with wireless transducers and a mobile device, a single operator using a 490W can monitor and balance a hydronic system in less time and with less manpower than would be possible using a traditional hydronic balancer. In addition, being wireless, the 490W has zero hoses or manifolds – meaning there are no annoying attachments that need to be carried, that can snag onto equipment, or that need to be drained between readings. Continue reading “On the Job with Dwyer: Series 490W Wireless Hydronic Differential Pressure Manometer”