Selecting the correct flowmeter can be a challenging task, and the variety of flow technology options can make the decision even more difficult. By keeping the benefits and drawbacks of each type in mind, you will be able rest easy knowing you’ve made the best choice for your application.
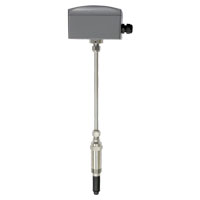
1. Electromagnetic
Electromagnetic flowmeters, often called magmeters, provide continuous flow indication of liquids via state-of-the-art electromagnetic technology based on Faraday’s Law. Because of this, magnetic flowmeters only work with fluids that are conductive. These flowmeters have no moving parts to wear or jam, offer low pressure drop, and generally require less maintenance than other types of flowmeters. They also have a wide sensing range and offer highly accurate readings.
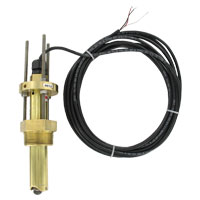
2. Paddlewheel
Paddlewheel flowmeters measure liquid flow rate with a rotating impeller, which is designed to provide a pulse when passing a magnetic or optical sensor. These units offer high accuracy and fast response time, while remaining cost-effective for a variety of applications. These mechanical-type flowmeters are ideal for applications where the media temperature varies or when the material being monitored is magnetic, such as in the oil and gas or utilities industries.
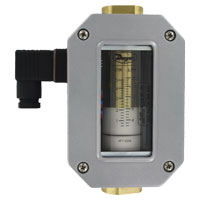
3. Turbine
Turbine flowmeters utilize a simple working principle based on a bladed rotor that rotates in correlation with the speed of the fluid passing through the meter. These meters are typically economical and easy to install. The simple but durable construction provides reliable performance for liquid and gas flow measurement. They prove to be most effective in applications with steady, high-speed flows.
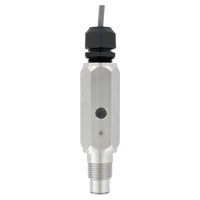
4. Thermal Dispersion
Thermal dispersion flowmeters use a temperature element that is heated up beyond the media temperature, and the flow rate is determined from the rate at which the probe cools. There are no moving parts to wear or break, providing better long-term reliability than a paddlewheel or turbine flowmeter and the omni-directional sensing offers easy installation without concerns of flow alignment. In addition, the meter only needs to be inserted 10% into the flow, reducing the pressure drop. This technology is well-suited for applications where the pipe might be empty at times, as the active heating and cooling element helps it to remain unaffected.
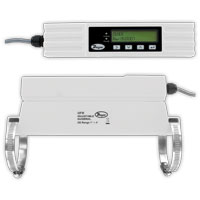
5. Ultrasonic
Ultrasonic flowmeters measure flow by transmitting and receiving ultrasound waves within a pipe. No moving parts are needed, meaning there’s no pressure drop across the flowmeter and minimal maintenance is required, which allows these to be used in applications with sediment or other floating solids in the liquid. Optional clamp-on flowmeters offer even greater ease-of-use by eliminating the need to cut a pipe, preventing risk of leakage, and ensuring that the meter will not come in contact with the fluid being measured, which is ideal for applications where potable water is being monitored.
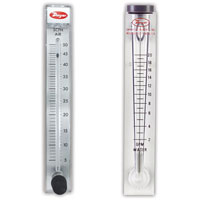
6. Variable Area
Variable area flowmeters, or rotameters, are some of the most commonly used flowmeters in the industry. They feature a simple construction that requires no power, providing cost-effective and reliable flow measurement. Their ability to be used with liquids and gases and no upstream/downstream straight piping requirements gives them the flexibility to be used in a variety of flow applications, including laboratories, medical equipment, and industrial applications.
In conclusion, it’s important to consider the advantages and disadvantages of each technology when selecting the best flowmeter for your application. To learn more about Dwyer’s product line of flow measurement instrumentation, please visit http://www.dwyer-inst.com/Product/Flow/