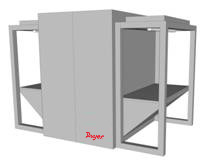
There are many manufacturing processes that require human operators to perform tasks, which can create hazardous levels of particulate, fumes, gases, vapors, and mists. A few of these processes include: welding, sanding, grinding, brazing, laser cutting, tempering, and quenching. The Occupational Safety and Health Administration (OSHA) has regulatory requirements to reduce worker’s exposure to these hazards, which can cause respiratory and other health issues. Downdraft tables are workstations designed to better protect the operators who perform these tasks, in a bench top setting, by removing the hazardous material that laden the air from the worker’s breathing zone.
There are many sizes and configurations of downdraft tables, with varying degrees of control that could be incorporated. The most basic designs would simply incorporate a fan or blower running at 100%, powered to pull air and particulates down and away from the workstation area/operator. Depending on the process and the size of the particulates created, the suspended solids may be allowed to drop out of the airstream (via gravity) with the excess air volume exhausted. In most cases, these finer particles in the air would be pulled through various filters. Basic designs would require the user to periodically check and change these filters as they will eventually become too dirty and inefficient.
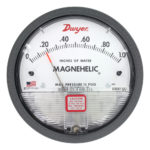
The first application that arises for Dwyer® products is the monitoring of these filters in order to notify the operator when they need to be cleaned or changed. This can be accomplished by measuring the differential pressure drop across the filter, which will increase as the filter collects more particles from the airstream. The filter manufacturer determines a maximum recommended pressure drop for when they will consider the filter dirty. This can be monitored with the Dwyer® Magnehelic® or Minihelic® differential pressure gage to ensure the system runs at maximum filter efficiency while reducing downtime for unnecessary filter cleanings or change outs. Some systems may also utilize digital indication for this function, and the Dwyer® DigiMag® gage would be a good solution for those applications.
In order to greatly reduce or eliminate the need for manual cleaning of the filters, many downdraft table manufacturers have incorporated self-cleaning filtration systems. These self-cleaning systems utilize compressed air that is pulsed across the filters to knock the dust and particulate matter off the filter media. From there it can be collected in bins that would periodically be cleaned. For production facilities that have a large number of downdraft workstations, the particulate waste can be moved away automatically by a pneumatic conveying system or mechanical auger.
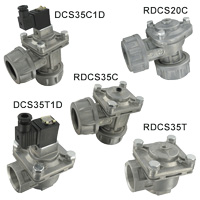
There are several applications for Dwyer® products within these self-cleaning type systems. The pulses of air used to clean the filters have to be controlled by sequencing diaphragm pulse valves, either open or closed. As the valves open, they allow the burst of pressurized air to pass through to a single filter or a bank of filters, cleaning off the built up particulate before the valve closes. Dwyer offers springless diaphragm valves in our Series DCS/RDCS, which provide more durability and reliability by eliminating the mechanical wear associated with spring-type valve designs.
The diaphragm valves are sequenced to ensure there is sufficient compressed air available to properly clean the filters. This can be accomplished with the use of Dwyer’s pulse timer boards. Our Series DCT timer boards control the amount of time each valve is open, the amount of time before the next valve pulse, and the amount of time before the sequence starts again. Some self-cleaning filter systems used in downdraft tables will clean continuously, be initiated manually by an operator, or work on a periodic cycle while running during the system’s downtime.
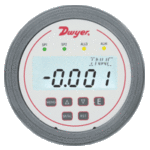
The need for more energy and filter efficient designs has created a market for higher-end systems that utilize on-demand cleaning. In these systems, the timer boards are initiated at a preset differential pressure so the filters are only cleaned when they need it. This reduces total air consumption and increases the filter’s longevity, due to the fact that they are only cleaned when they reach the optimal pressure drop. This type of on-demand control would require a separate differential pressure switch like the Dwyer® Photohelic® switch/gage and Digihelic® controller or a timer board that incorporates the pressure module like the DCT1000 Series. For additional information on continuous versus on-demand cleaning with Dwyer timer boards, please read our article on “Dust Collector Timer Controllers.”
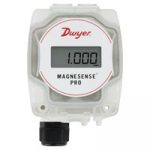
As the demand for higher energy efficiency and operator safety continues to increase, more downdraft table manufacturers are also incorporating variable frequency drives (VFD’s) to control their system’s blower motor. Without a VFD in place, the blower would run at 100% of its capacity and energy consumption, when the system was in operation. Utilizing a VFD allows the blower to run at lower speeds based on the system’s demand to meet minimum airflow requirements for operator safety while reducing the overall energy consumption. Dwyer’s Series MSX and Series MSX Pro Magnesense® differential pressure transmitters can be used to provide the feedback for VFD controlled systems.
If you have any questions, the Dwyer Applications Engineers are available to assist by phone at (219) 879-8868 x6402, or by email at tech@dwyermail.com.