There are two common ways to measure air velocity: by using pressure-based instrumentation or by using temperature-based instrumentation. Before we discuss the different technologies available for measuring velocity pressure, it is important to understand the basics of air velocity.
Air velocity is the area of air movement measured in distance traveled relative to time elapsed. It is commonly measured in meters per second (m/s) or feet per min (ft/min).
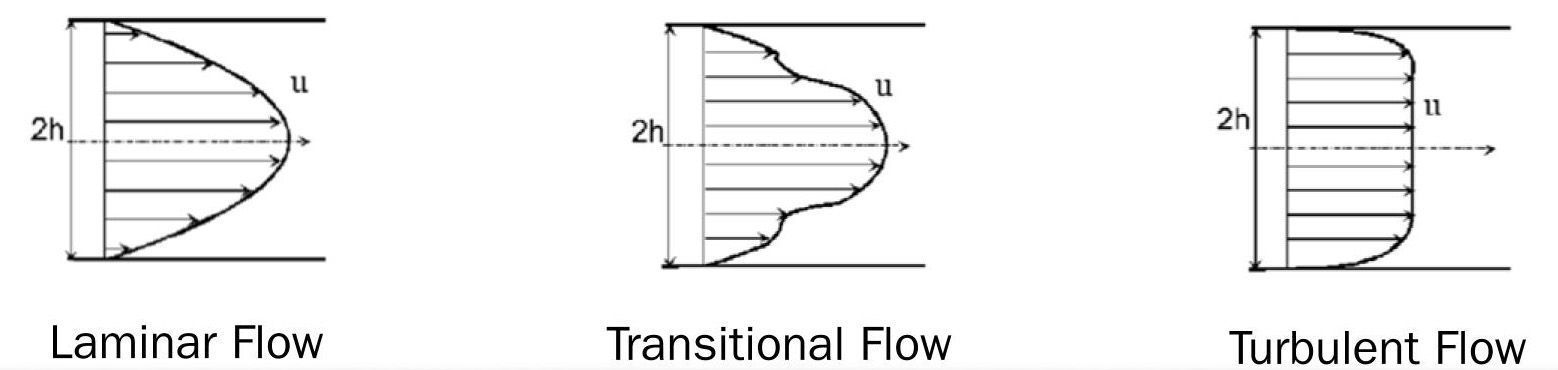
There are three types of flow profiles found when monitoring air velocity: laminar, transitional, and turbulent flow. Laminar flow is characterized by smooth movement, while turbulent flow is characterized by irregular movement or fluctuation. Laminar flow can become transitional or turbulent by introducing an elbow in the ductwork, which turns the air. This post will be focused on the laminar flow profile.
Pressure-Based Instrumentation
The Bernoulli equation, which accounts for air density, static pressure, and total pressure, is key to pressure-based velocity measurements.
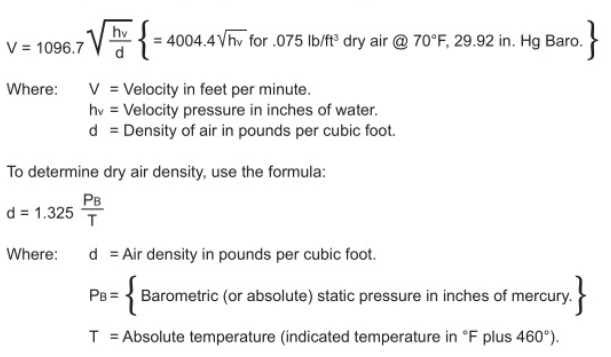
To use pressure to calculate air velocity, two separate sensors are required. One sensor measures static pressure, or the pressure pushing against the ductwork, and the other measures total pressure, or the pressure induced from flow moving through the ductwork.
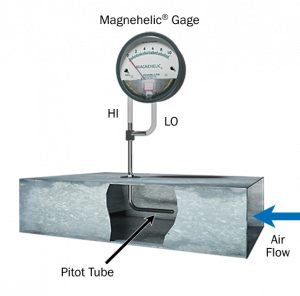
Typically, pitot tubes are used for pressure measurement. A pitot tube is a tube within a tube. The inner tube monitors static pressure and the outer tube has holes drilled into it to measure static pressure. One pitot tube will give the difference between total and static pressure, which is the velocity pressure. Then, the Bernoulli equation will be used to calculate the air flow converting velocity pressure (in inch w.c.) to a usable air flow in ft/min at standard conditions.
Temperature-Based Instrumentation
Anemometers are used to calculate air velocity by temperature. King’s Law is at the root of temperature measurement and mathematically describes heat transfer in air flow using a heated wire. When air moves over a wire, there is a loss of temperature and heat energy is removed. The change in heat energy can then be calculated using a wheatstone bridge to determine the resistance change, which is correlated to the speed of air moving across the sensor. An anemometer has two temperature sensors: one that provides a reference temperature, and one that measures the temperature of the air moving across the sensor. As the air velocity speeds up, more energy is lost. The loss in energy can then be used to calculate air velocity.
Advantages of Temperature-Based Instrumentation to Measure Air Velocity
During Dwyer’s research and development processes, we discovered several advantages to using temperature-based instrumentation when measuring air velocity. First, the Bernoulli equation does not account for changes in the viscosity of the air, which is problematic because viscosity constantly changes based on the temperature of the airflow. Second, we found that at slower air velocities, holes for static pressure pickup changed the flow profile around the pitot tube, changing the flow from laminar to turbulent.
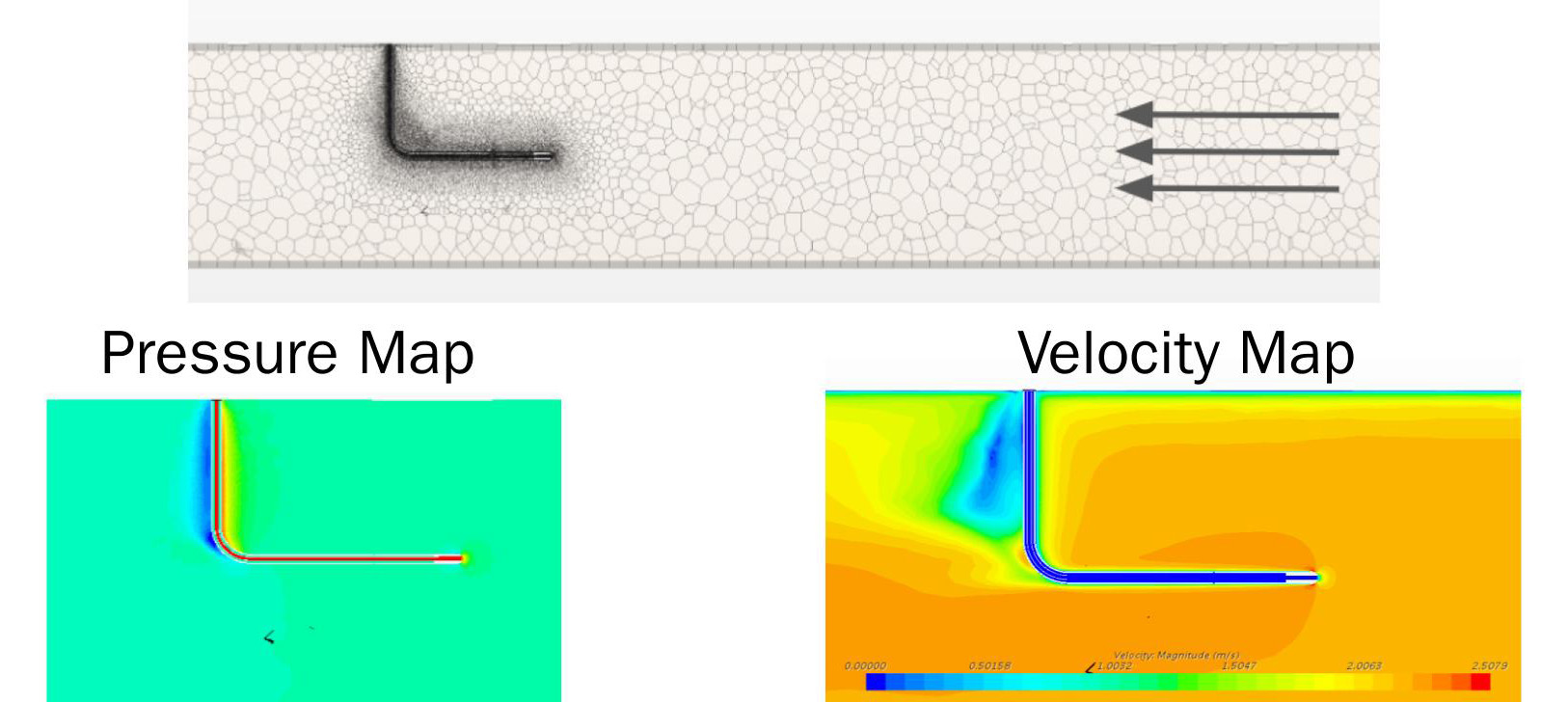
We found that pitot tubes are very accurate at high velocities, but have increased error at low velocities.
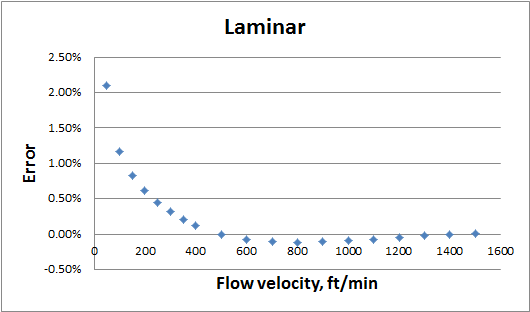
Another important consideration when choosing a measurement technology is your application. Most building management systems (BMS) and PLCs require a linear analog input, not a pneumatic input. This means that measurements obtained by pitot tubes must be converted using the Bernoulli equation. At low velocity pressures, an air velocity of 200 FPM yields a velocity pressure of 0.002 inches of water column. There are some specialized differential pressure sensors available that can measure this ultra-low pressure, but they are priced at a premium. Other technologies for measuring low flow, such as anemometers, are much more cost-effective.
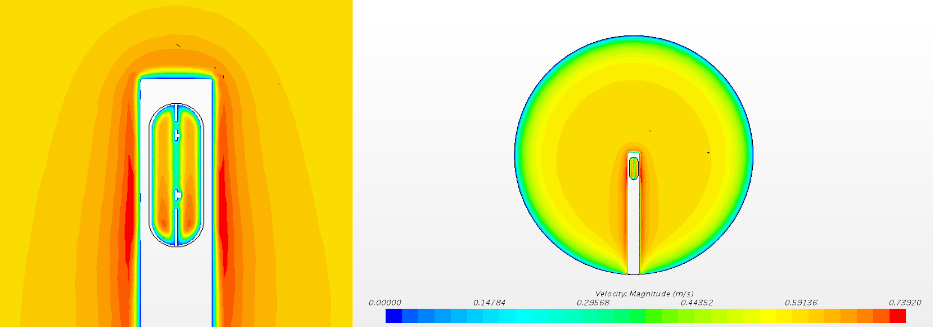
We found that when using temperature-based measurement, we can use sensor characterization to prevent some of the shortcomings of pressure-based measurement at low flow rates. Sensor characterization is the process of taking measurements from a sensor under controlled conditions and ensures a guaranteed level of readout accuracy over various operating conditions such as temperature, humidity, or atmospheric pressure. During our manufacturing processes, we use calibrated references to characterize our air velocity sensors for temperature and humidity changes in the air. Characterization ensures uniform sensor accuracy across a range.
Applications
Thermal anemometers are well suited for critical environments (such as hospital operating rooms) where air changes must happen frequently. When air is changed frequently, it must change at a very low velocity in order to reduce the risk of moving particulates and other contaminants and contaminating the air. Typical operating rooms have air velocities ranging from 37 FPM to 55 FPM. ANSI/ASHRAE/ASHE Standard 170-2013 requires a minimum of 4 Outdoor ACH (Air Changes/Hour) and a minimum of 20 Total ACH (Air Changes/Hour). An anemometer can be paired with a BMS to verify the minimum number of air changes in these low-flow critical environments to ensure ASHRAE standards are met.
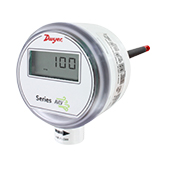
Thermal anemometers can also be used to measure air velocity rate in commercial applications, such as hotels, schools, stores, and offices. In these applications, velocities typically range from 1,000 to 3,000 FPM for main supply ducts and 500 to 1,500 FPM for branch supply ducts. By using the Bernoulli equation, we can calculate the velocity pressure of the air, which is typically 0.062 to 0.561 inches of water column for main ducts and 0.016 to 0.140 inches of water column for branch supply ducts. Given the higher flow ranges in commercial applications, pressure or temperature instruments can be used to measure velocity. But as explained above, pressure measurements must be converted from inches of water column to FPM. Some devices are programmed with the Bernoulli equation and will complete the conversion for you. If the equation is not preprogrammed in your device, your BMS or PLC will have to do the conversion from velocity pressure to usable velocity, increasing the risk of error.
Another advantage to using an anemometer is that they work off of a temperature principle. There is a temperature sensor that is monitoring the temperature conditions of the supply itself. You can get two measurements out of one device because you are typically able to measure both the temperature output and the air velocity output. The air velocity output will be linear to the flow range, which can be easily input to your BMS or PLC.
Summary
When measuring air velocity with pitot tubes, fluid viscosity is the root cause of error when measuring low flow rates. CFD models show local flow development changes around the sensor static pressure holes leading to increased error. For this reason, Dwyer recommends the practical limitation of 200 FPM for pitot tubes.
The sensor characterization process used when calibrating anemometers yields improved accuracy across varying process constraints by accounting for factors such as humidity, temperature, and pressure. CFD models show local flow development changes around the sensor that would lead to increased error without the integration of sensor characterization. The references used for sensor characterization lead to improved accuracy for target application velocities.
To learn about the Dwyer air velocity product line, please visit our website.